GRUNDFOS SERVICE INSTRUCTIONS
SQFlex pumping system
The SQFlex is a reliable water su pply system especially suitable
for remote locations not connected to the electricity supply grid. The
SQFlex system is equipped with the SQFlex submersible pump.
The SQFlex system is powered by renewable energy sources.
sqflex_SI_US_WG.book Page 1 Thursday, October 1, 2009 3:27 PM
= Page 1 =
2 / 60
Mission
- to successfully develop, produce, and sell high quality
pumps and pumping systems wo rldwide, contributing to a
better quality of life and healthier environment.
• One of the 3 largest pump companies in the world
• The second largest manufacturer of submersible motors in the world
• World’s largest manufacturer of circulator pumps
• World headquarters in Denmark
• North American headquarters in Kansas City - Manufacturing in Fresno, California
• 80 companies in 45 countries
• More than 16 million motors and pumps produced annually worldwide
• North American companies operating in USA, Canada and Mexico
• Continuous reinvestment in growth and development enables the company to
• BE responsible, THINK ahead, and INNOVATE
GBJ - Bjerringbro, Denmark
GMU - Fresno, California GPU - Olathe, Kansas
GMX - Monterrey, Mexico GPA - Allentown, Pennsylvania GCA - Oakville, Ontario
sqflex_SI_US_WG.book Page 2 Thursday, October 1, 2009 3:27 PM
= Page 2 =
Service instructions
SQFlex water supply systems
3 / 60
Table of contents
1. SQFlex components ........................................................................................................................ 4
1.1 Pumps................................................................................................................................................ 4
1.2 Motor.................................................................................................................................................. 7
1.3 Control and switch boxes................................................................................................................... 8
1.4 Solar modules.................................................................................................................................. 15
1.5 Wind turbine..................................................................................................................................... 18
2. Start-up ........................................................................................................................................... 22
3. Maintenance................................................................................................................................... 23
3.1 Solar modules.................................................................................................................................. 23
3.2 Wind turbine..................................................................................................................................... 24
4. Trouble-shooting ........................................................................................................................... 25
4.1 Solar-powered system..................................................................................................................... 27
4.2 Solar-powered system with CU 200 control unit and level switch ................................................... 29
4.3 Solar-powered system with generator back-up ............................................................................... 31
4.4 Wind-powered system ..................................................................................................................... 33
4.5 Wind-powered system with CU 200 control unit and level switch.................................................... 35
4.6 Combined system............................................................................................................................ 37
4.7 Combined system with CU 200 control unit and level switch .......................................................... 39
4.8 Options with generator as back-up source ...................................................................................... 41
5. Service of pump and motor .......................................................................................................... 43
5.1 General information ......................................................................................................................... 43
5.2 Service tools .................................................................................................................................... 44
5.3 Torques and lubricants .................................................................................................................... 46
5.4 Helical pump type ............................................................................................................................ 47
5.5 Centrifugal pump and motor ............................................................................................................ 48
5.6 Centrifugal pump type with splined shaft......................................................................................... 49
5.7 Centrifugal pump type with cylindrical shaft..................................................................................... 50
5.8 Checking and replacing wear parts of centrifugal pumps ................................................................ 51
5.9 Testing the pump by means of CU 200 SQFlex control unit............................................................ 52
sqflex_SI_US_WG.book Page 4 Thursday, October 1, 2009 3:27 PM
= Page 3 =
4 / 60
1. SQFlex components
1.1 Pumps
Two pump types are used, the helical rotor pump type and the centrifugal pump type.
Nameplate, helical rotor pump
The nameplate is engraved into the pump sleeve.
Key to nameplate, helical rotor pump
TM02 6973 2103
Fig. 1 Nameplate, helical rotor pump
Pos. Code Description
1 PROD. NO. 96078012 Product number
MODEL A Pump generation
P1 0110 Production code - Bjerringbro (P1) + production year and week
2 xx SQF - x Type designation, see section Type key on page 6
3 • Weight: x,x kg
• MADE IN DENMARK
• CE
• Pump net weight
• Country of origin
• Mark of approval.
4 Rp 1 1/4 Type and size of connecting thread
1
2
3
4
sqflex_SI_US_WG.book Page 4 Thursday, October 1, 2009 3:27 PM
= Page 4 =
5 / 60
Nameplate, centrifugal pump
The nameplate is attached to the suction interconnector.
Key to nameplate, centrifugal pump
TM02 6974
Fig. 2 Nameplate, centrifugal pump
Pos. Code Description
1 Type 60 SQF -3 Type designation, see section Type key on page 6
2 MODEL A Pump generation
3 96078070 Product number
4 Q m³ Rated flow rate (not indicated)
5 Weight 4.9 kg Pump net weight in kg
6 CE Mark of approval
7 0140 Production year and week
8 n min -1 Speed (not indicated)
9 H Head at rated flow rate (not indicated)
984457
60 SQF 3
sqflex_SI_US_WG.book Page 5 Thursday, October 1, 2009 3:27 PM
= Page 5 =
6 / 60
Type key
The type key is common for helical rotor pump and centrifugal pump.
Centrifugal pumps come in two main types: with splined pump shaft and with cylindrical pump shaft.
25 SQF-3 and 25 SQF-6 have a splined pump shaft. 40 SQF-3 and 60 SQF-3 have a cylindrical shaft.
X SQF-X
Rated flow rate in US GPM at 3000 min-1 (approximate value)
• 3 = helical rotor pump
• 6 = helical rotor pump
• 11 = helical rotor pump
• 25 = centrifugal pump
• 40 = centrifugal pump
• 60 = centrifugal pump
Type range
Number of stages
sqflex_SI_US_WG.book Page 6 Thursday, October 1, 2009 3:27 PM
= Page 6 =
7 / 60
1.2 Motor
The MSF 3 motor is a sealed construction made of stainless steel. It is a brushles, electronically
commutated DC-motor with a permanent-magnet rotor.
Nameplate, motor
The nameplate is engraved into the stator sleeve.
TM02 2452 0202
Fig. 3. Nameplate, motor
Key to nameplate, motor
Pos. Code Description
1 MSF 3 Type designation
2
PROD. NO. 96040989 Product number
MODEL A Pump generation
P1 0110 Production code - Bjerringbro (P1) + production year and week
3
VDC: 30-300 V
VAC: 1 x 90-240 V
The motor can be supplied with either DC or AC voltage:
• DC: 30-300 V or
• AC: 1 x 90-240 V
P1: 0.9 kW Maximum input power [kW]
I: 7 A Maximum input current [A]
S1/40 C Suitable for continuous operation up to 40×C
4
CONT. DUTY 104F Suitable for continuous operation at 104°F
Ins Cl F Code A Insulation class F. Start-kVA is 0-3.15 per hp
5 PF 1.0 RPM 500 - 3600 Power factor = 1. Rated speed 500 - 3600 rpm
6 IP 68 150 m Enclosure class: IP 68. Max submerged depth: 150 m
Weight 6.55/14.4 kg/lb Motor net weight in kg and pounds
7
THERMALLY PROTECTED Temperature sensor built into the electronic unit
MADE IN DENMARK Country of origin
CE Mark of approval
MSF 3
500-3600
sqflex_SI_US_WG.book Page 7 Thursday, October 1, 2009 3:27 PM
= Page 7 =
8 / 60
1.3 Control and switch boxes
1.3.1 CU 200 SQFlex control unit
The CU 200 SQFlex control unit offers:
• system monitoring on the basis of sensor signals
• system control on the bas is of sensor signals
• monitoring of pump operation and alarm indication.
Internal (and external) wiring of CU 200 SQFlex control unit
Technical data
• 30-300 VDC, PE.
• 1 x 90-240 V –10%/+6%, 50/60 Hz, PE.
Maximum load: 100 mA.
sqflex_SI_US_WG.book Page 8 Thursday, October 1, 2009 3:27 PM
= Page 8 =
9 / 60
CU 200 SQFlex display and indicator lights
The front cover of CU 200 features a button and various indications:
ON/OFF button
• Green light on: The system has
been switched on.
• Red light on: The system has
been switched off.
• Both lights off: The system
lacks the required power to
light the display.
• Flashing green light: The sys-
tem has adequate power to
light the display but lacks suffi-
cient power to start the pump.
Full water reservoir
The yellow light
indicates that the
water reservoir is full. Pump operation
A running green light in-
dicates that the pump is
operating at more than
500 rpm.
Fault indicator
Red light indicates fault.
Dry running
Red light indi-
cates lack of
water.
Power and fault codes
The display indicates 0 Watt
until the power supply is suf-
ficient to run the pump at
500 rpm; upon startup, the
power consumption of the
pump is indicated in kW.
When the fault indicator is
on, the display indicates fault
codes, see Trouble-shooting
by means of CU 200 on page
10.
F1 = overvoltage
F2 = overtemperature
F3 = no contact to the pump
F4 = overload
sqflex_SI_US_WG.book Page 9 Thursday, October 1, 2009 3:27 PM
= Page 9 =
10 / 60
Trouble-shooting by means of CU 200
Indication/Fault Possible cause Remedy
1. No light in front
cover.
Pump does not
deliver water.
No voltage supply. • Reestablish the voltage supply.
Position of ribbon cable
connector is wrong or
cable is defective.
• Correct the position of the cable or replace it.
2. No light in front
cover, and pump
does not deliver
water. But the LEDs
inside CU 200 indi-
cating 5 V, 10 V and
24 V internal supply
voltage are on, and
the ‘CONTROL
INDICATOR’ LED is
not flashing.
CU 200 is defective. • Replace the CU 200.
3. Pump does not start.
Green indicator light
in ON/OFF button is
on.
No fault indicated.
CU 200 or pump is defec-
tive.
• Check that the ‘CONTROL INDICATOR’ LED is
flashing. If not, replace the CU 200.
• Check that there is sufficient voltage on the
PUMP terminals. If no voltage can be measured,
replace the CU 200.
If a supply voltage to the pump can be detected,
continue as follows:
• Switch off the energy supply and wait for one
minute.
• Switch on the energy supply and observe what
happens:
If the green indicator light in the ON/OFF button
is on and the pump still does not start, the pump
or pump cable is defective.
• Repair or replace pump or cable.
4. Off light in the ON/
OFF button is on. Pump has been stopped. • Press the ON/OFF button on the CU 200 to start
the pump.
5. CU 200 indicates
‘F3 = no contact to
pump’.
CU 200 defective. • Check
- the connection in the CU 200
- the pump cable
- the end cover with socket on the pump.
Pump cable or connec-
tions defective.
Pump is defective. • Repair or replace the pump.
6. CU 200 indicates
‘F1 = overvoltage’
Supply voltage is above
permissible range.
• Disconnect the solar modules to allow the volt-
age to drop.
• Reconfigure the modul es and reconnect them.
If a different supply sour ce is used, check that
the voltage is within the recommended voltage
range.
Note: As the voltage is detected at the motor, allow
for the voltage drop in the pump cable.
7. CU 200 indicates
‘F2 = overtempera-
ture’.
Too high water tempera-
ture.
• Ensure that the water te mperature is below the
maximum permissible level.
Incrustations on motor. • Remove incrustations on the motor.
Pump is defective. • Repair or replace the pump.
sqflex_SI_US_WG.book Page 10 Thursday, October 1, 2009 3:27 PM
= Page 10 =
11 / 60
8. CU 200 indicates
‘F4 = overload’.
Too low input voltage. • Increase the supply voltage, to 30 VDC or
higher.
Pump is defective. • Repair or replace the pump.
Only helical rotor
pumps. Pumped liquid is
contaminated with oil or
similar substance.
• Clean the liquid and replace the pump.
Motor liquid low / Missing. • Check or refill motor liquid.
9. Green indicator light
in ON/OFF button is
flashing.
Insufficient power supply. • Increase the number of solar modules or con-
nect an alternative energy supply, such as wind
turbine, batteries or generator.
Pump has seized up. • Clean the pump.
10.Running light on CU
200 but low wattage.
System not grounded. • Check system for adequate grounding
Pump is defective. • Repair or replace the pump.
If a centrifugal pump is us ed: Check that the riser
pipe is not blocked.
11. No light in front
cover. Pump delivers
water.
CU 200 is defective. • Replace the CU 200.
Ribbon cable not
mounted.
• Mount the ribbon cable.
12.Pump does not stop
when water reservoir
is full.
Fault indicator light
on CU 200 is off.
Level switch is dirty or
defective.
• Clean or replace the level switch.
Cable on level switch is
damaged.
• Replace the cable.
13.Pump does not stop
when water reservoir
is full.
Fault indicator light
on CU 200 is on.
CU 200 is defective. • Replace the CU 200.
14.Pump does not start
when water reservoir
is empty.
Water reservoir indi-
cator is on.
Level switch is defective. • Replace the level switch.
Cable on level switch is
damaged.
• Replace the cable.
CU 200 is defective. • Replace the CU 200.
Indication/Fault Possible cause Remedy
sqflex_SI_US_WG.book Page 11 Thursday, October 1, 2009 3:27 PM
= Page 11 =
12 / 60
1.3.2 IO 50 SQFlex switch box
Technical data:
DC: Max. 225 V, PE.
AC: Max. 265 V, 50/60 Hz, PE.
The IO 50 enables manual starting and stopping of the
pump in a solar-powered SQFlex system. In addition, the
IO 50 functions as a connection point for all necessary ca-
bles.
Internal (and external) wiring of IO 50 SQFlex switch box
sqflex_SI_US_WG.book Page 12 Thursday, October 1, 2009 3:27 PM
= Page 12 =
13 / 60
1.3.3 IO 101 SQFlex switch box
Technical data:
• DC: Max. 225 V, PE.
• AC: Max. 265 V, 50/60 Hz, PE.
The internal relay in the IO 101 has the following rated voltage:
• 115 V –15%/+10%, 50/60 Hz, PE.
The IO 101 SQFlex switch box makes it possible to
• switch off the voltage supply to the pump and
• connect a back-up generator.
A back-up generator is useful in periods of insufficient
solar energy or in case of an immediate requirement
for water supply or a need for water at night.
Internal (and external) wiring of IO 101 SQFlex switch box
sqflex_SI_US_WG.book Page 13 Thursday, October 1, 2009 3:27 PM
= Page 13 =
14 / 60
1.3.4 IO 102 SQFlex breaker box
The IO 102 is applicable in SQFlex systems powered ex-
clusively by a wind turbine
The IO 102 SQFlex breaker box makes it possible to
• switch off the voltage supply to the pump, and
• Stop the wind turbine blades
• connect solar modules as well as a wind turbine.
The IO 102 is applicable in SQFlex systems provided
the system voltages ment ioned below are not ex-
ceeded.
IO 102
Technical data:
• DC: Max. 225 V, PE
• AC: Max. 265 V, 50/60 Hz, PE.
Internal (and external) wiring of IO 102 SQFlex breaker box
sqflex_SI_US_WG.book Page 14 Thursday, October 1, 2009 3:27 PM
= Page 14 =
15 / 60
1.4 Solar modules
Positioning
Solar modules located in the northern hemisphere should face south. Use a compass to position the mod-
ules as precisely as possible. Due to the magnetic de clination it may be necessary to turn the modules some
degrees away from the direction of the compass. In case of positive declination, turn the modules some de-
grees to the west, in case of negative declination, turn the modules some degrees to the east. See Fig. 4.
Solar modules located in the southern hemisphere should face north. Use a compass to position the mod-
ules as precisely as possible. Due to the magnetic de clination it may be necessary to turn the modules some
degrees away from the direction of the compass. In case of positive declination, turn the modules some de-
grees to the east, in case of negative declination, turn the modules some degrees to the west. See Fig. 4 .
Fig. 4. The map illustrates the differences in magnetic declination in different parts of the world. Declination is
caused by the fact that the geographic north pole and th e magnetic north pole are not lo cated in the same place.
Depending on your location on the globe you must turn t he solar modules away from the direction of the com-
pass. How much appears from the map.
Mounting
The solar modules must be mounted on a support structure.
When mounting the solar modules, make sure that the mo dule frames overlap in orde r to allow for rain water
to run off.
For further information on the installation of solar modules, see installation and operating instructions for the
modules.
Tilt angle
For maximum utilisation of t he solar radiation the tilt angle of the support structure can normally be adjusted
from 15° to 45°.
180°
60°
30°
0°
-30°
-60°
60°
30°
0°
-30°
-60°
210° 240° 270° 300° 330° 0° 30° 60° 90° 120° 150° 180°
180° 210° 240° 270° 300° 330° 0° 30° 60° 90° 120° 150° 180°
sqflex_SI_US_WG.book Page 15 Thursday, October 1, 2009 3:27 PM
= Page 15 =
16 / 60
1.4.1 GF 80 solar modules
Visual inspection of solar modules
• Check that the solar modules are intact.
• Make sure that trees, grass, bushes, buildings, etc. do not cast a shadow on the solar modules.
Electrical connection GF 80 solar modules
Note: Before making any electrical connections, make sure that the solar modules are covered with a
non-transparent covering material to ensure that the modules are dead.
• The cover must be removed before measuring is made.
• Measurements must be made when the solar modules are not connected.
• The current to be measured is the short-circuit current ISC.
The GF 80 solar modules are equipped with plugs and sockets for easy
connection of several modules in parallel or series. The solar modules must
be mounted on a support structure, tilted at an angle ensuring optimum
utilization of the solar energy.
This module is UL, Tüv, CE and IEC 61215 approved.
GF 80
Peak power (PMax) 80 W
Voltage (Vmp) 33.3 V
TM04 5085 2609
Current (Imp) 2.4 A
Open circut voltage (Voc) 41.5 V
Short circut current (Isc) 2.6 A
Reference cell temperature
(Tcref) 25 °C
Solar irradiation at reference
cell temperature (Itref) 1000 W/m2
sqflex_SI_US_WG.book Page 16 Thursday, October 1, 2009 3:27 PM
= Page 16 =
17 / 60
Electrical connection GF 80 solar modules (continued)
The solar panels must be connected to earth via a Protective Earth (PE) conductor
Note: To achieve good earth connection and thus to protec t persons, it is of decisive importance to fit
the earth clips and earth terminals
Cable sizing chart
Note: max. cable length in feet; uses a max. 3 % voltage drop
Max. cable length between CU200 and SQF = 650 ft.
SQ Flex is most efficient at 120V and above. Grundfos recommends combining panels to produce 120
or above.
TM02 8643 0604
Panels Power
(Wp)
Volts
(Vmp)
Amps
(lmp)
Volts
(Voc)
Amps
(lsc)
14
AWG
12
AWG
10
AWG series parallel
1 80 33 2.4 42 2.6 82 130 207 1
2 160 67 2.4 83 2.6 164 261 415 2
3 240 100 2.4 125 2.6 246 391 622 3
4 320 133 2.4 166 2.6 328 522 829 4
5 400 167 2.4 208 2.6 410 652 1037 5
6 480 200 2.4 249 2.6 493 783 1244 6
7 560 233 2.4 291 2.6 575 913 1451 7
8 640 266 2.4 332 2.6 657 1044 1659 8
8 640 133 4.8 166 5.2 164 261 415 4 2
9 720 100 7.2 125 7.8 82 130 207 3 3
10 800 167 4.8 208 5.2 205 326 518 5 2
12 960 200 4.8 249 5.2 246 391 622 6 2
14 1120 233 4.8 291 5.2 287 457 726 7 2
15 1200 167 7.2 208 7.8 137 217 346 5 3
16 1280 133 9.6 166 10.4 82 130 207 4 4
18 1440 200 7.2 249 7.8 164 261 415 6 3
1
2
3
7
1
2
3
7
1
2
1
2
sqflex_SI_US_WG.book Page 17 Thursday, October 1, 2009 3:27 PM
= Page 17 =
18 / 60
1.5 Wind turbine
Values measured between the three phases must be identical.
TM04 5087 2609
Wind turbine
voltage [VAC]
IO 102
voltage [VDC]
Breaker Box IO 102
V mA
A V
OFF
mV
160
A
V COM A mA A
A mA A COM V
A
160
mV
OFF
V A
mA V
V mA
A V
OFF
mV
160
A
V COM A mA A
A mA A COM V
A
220
mV
OFF
V A
mA V
VDC
Measurement of VAC and VDC
VAC
m/s
mph
m/s
mph
sqflex_SI_US_WG.book Page 18 Thursday, October 1, 2009 3:27 PM
= Page 18 =
19 / 60
1.5.1 Trouble-shooting
1. Find out if the problem is mechanical or electrical.
• Propeller cannot turn = Mechanical problem, see Mechanical problems on page 20.
• Propeller turns slowly = Electrical problem, see Electrical problems on page 21.
Electrical problems may be in the wind turbine or the IO 102 breaker box. Determine which as follows:
2. Disconnect the three wires from the wind turbine one at a time at the IO 102 breaker box. If the propel-
ler starts, the wire that allowed it to start leads to a defective rectifier in the IO 102 breaker box. Replace
the breaker box, see Overview of possible system combinations on page 26.
3. If the propeller still does not start, the problem is in the tower wiring or the wind turbine.
4. The propeller is running, but may have an electrical problem. Using a voltmeter, read the voltage
across the leads and see the list below as a guide to possible problems.
• The voltage increases and decreases slowly with wind speed and equally across all wires = Every-
thing OK.
• No voltage across two wires = One wire from wind turbine is not carrying power. Check in order:
-the tower wiring to ensure it is properly wired.
-slip rings and brushes,
-stator connections and stator windings for obvious damage.
• The voltage is significantly higher across two wires than the others = Contact the distributor or the fac-
tory.
• Voltage is produced even after ON/OFF switch is activated = Possibly a faulty ON/OFF switch or a
wire has been short circuited to the other two wires or an internal fault has occurred in the IO 102
breaker box.
• The voltage is significantly lower across two wires than the others = Bad connection at the wind tur-
bine voltage connections or faulty stator winding.
5. Should these steps not solve the problem, proceed directly to Electrical problems on page 21.
Wind turbine power outpout
Instantaneous speed
1000
800
600
400
200
0
5 10 15 20 25 30 35 40 mph
2.3 4.5 6.8 9.0 11.3 13.5 15.8 18.0 m/s
Instantaneous Wind Speed
Power Output (W)
Whisper 200
sqflex_SI_US_WG.book Page 19 Thursday, October 1, 2009 3:27 PM
= Page 19 =
20 / 60
Mechanical problems
Fault Cause Remedy
1. Propeller is stationary, even in
high winds.
• Ice in wind turbine, or uneven
ice on propeller.
• Debris between rotor and stator.
• Loose magnet.
• Worn-out bearing.
• Remove ice, or wait for warm
weather.
• Turn propeller gently by hand
and blow or use piece of paper
to dislodge debris.
• Contact distributor.
• Contact distributor.
2. a) Propeller will not turn at all
except in high wind
b) Scraping or rubbing sound at
low rpm
c) Propeller always stops in the
same position.
• Same as above.
• Swelled wire keepers due to
high moisture.
• Same as above.
• Contact distributor.
3. a) Propeller is difficult to start
b) Output is low
c) more propeller noise than
usual.
d) Propeller seems out of balance.
• Ice on blade.
• Dirty blade.
• Split, warped or damaged
blade.
• One or more blades fitted
wrongly.
• Remove ice, or wait for warm
weather.
• Clean with soap or bug
cleaner.
• Replace broken or damaged
blade.
• Fit blade(s) correctly.
4. Propeller turns a little, but never
starts properly.
• Blades
Grundfos SQFlex Service and troubleshooting guide ( Text Only)
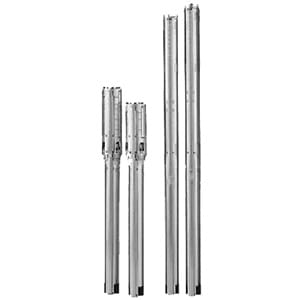