1
Flowlight
Booster Pump®
and
Solar Slowpump™
Installation & Service Manual
© 2003 by Dankoff Solar Products
__________________________________________________________________________
IMPROPER INSTALLATION WILL DAMAGE YOUR PUMP AND VOID YOUR WARRANTY
This manual is based on 20 years of experience with over 5000 pumps sold. We are pleased to
observe how few problems arise when our pumps are properly installed and maintained.
Please read and save this manual!
RECORD your MODEL # ______ - ___ SERIAL # _______
Verify your purchase: Please check Specification Sheet at the end of this manual, to verify
that the pump you received is the best model for your application. If it is not, please contact
your dealer or the factory for correction BEFORE installing your pump.
This manual covers two similar product lines:
• Solar Slowpump for water lift, powered by battery or solar-direct power, and
• Flowlight Booster Pump for water pressurizing, powered by battery system only.
Rear Cap
of Motor
Electrical Cable
Brush Holders
(one on each side ) Shaft Coupler “Rear” “Front”
Mounting Foot
Round
Plate
Dry Run
Switch
(optional)
clamps here
Note: Slow pum ps of the1400 and
2600-Series, and 115 Volt AC
have different mountin g
structure.
Motor Pump Head
——— INDEX IS INSIDE BACK COVER ———
= Page 1 =
2
BASIC CONSTRAINTS
I. PUMP MUST NOT BE SUBMERSED
II. WATER MUST BE FILTERED ABSOLUTELY CLEAN
III. PUMP MUST NOT RUN DRY
I. NON-SUBMERSIBLE PUMPS
Your pump must NOT be submerged in water, or rained or dripped on. If it is installed outdoors,
supply some weather protection, such as a sheet-metal shield or even a dog house – something
to keep it dry and also to protect it from the sun’s heat.
II. FILTRATION REQUIREMENT
Your pump is a PRECISION MACHINE. Traces of sand, clay, rust or other solids will cause
rapid wear or immediate damage, just as they would in your automobile engine. If your water is
CRYSTAL-CLEAR ALL THE TIME, our Fine Intake Strainer will provide sufficient protection. If
you have an intake strainer already, it is probably not fine enough -- openings must be no more
than several hairs wide, or additional filtration is required. Since water conditions are subject to
change, it is good insurance to use a filter regardless. Many dealers refuse to sell our pumps
without a filter since it minimizes call-backs.
Our 30-INCH INTAKE FILTER/FOOT VALVE is necessary for pumps lowered into wells.
Otherwise our INLINE FILTER is best, installed close to the pump's intake. If filters are
expected to clog often, maintainance may be minimized by plumbing two or more filters in
parallel. The INLINE FILTER has a clear bowl so its condition may be observed. KEEP SPARE
CARTRIDGES HANDY!
FILTER CARTRIDGES are available from your dealer or the factory. 9 7/8-inch cartridges for
the INLINE filter may also be obtained from local water system suppliers. The 5 or 10-micron
"spun polypropylene" type is best. Paper filters have less capacity. The kind that look like string
has more restance to flow. Carbon taste and odor cartridges have less capacity for dirt, more
resistance to flow, and cost more. Use them only if you have taste and odor problems.
A filter cartridge may look clean and still be clogged, due to fine silt embedded in the fibers. If
the pump becomes increasingly noisey over time, it is usually due to a clogging filter cartridge.
On the other hand, a cartridge that looks discolored may not be clogged. As long as your pump
runs quietly, the filter is OK. Use pump noise to indicate the need to change cartridges.
IRON PIPE OR FITTINGS will introduce abrasive rust particles if installed on the intake side of
the pump (they rust, even if galvanized). Pipe that is dirty inside (even new pipe) or has mineral
deposits in it will also introduce dirt. Dirt is introduced as pipe joints are assembled, especially
in a trench. Therefore, make sure inlet lines and fittings are FLUSHED CLEAN before hooking
up to pump.
The INLINE FILTER may have a red push-button valve to release pressure for maintenance. If
filter is placed more than a few feet higher than water source (at lowest level) the suction may
pull the valve open and introduce air. Prevent this by sealing around the push-button with
silicone sealant or epoxy, or replace the button with a nut, tightened down.
= Page 2 =
3
III. PUMP MUST NOT RUN DRY
Water is the lubricant for your pump. If it runs completely dry, it will overheat and fail.
DRY RUN SWITCH is an optional accessory to prevent damage from dry run. It is a small
device with two wires that attaches to the front of the pump. It senses temperature, and
switches the pump off before it gets too hot. If you are pumping from a tank, cistern or any
water source that can run low accidentally, a Dry Run Switch should be used. If it saves a
failure once in 10 years, it's worthwhile.
WARNING The dry run switch must be clamped tightly to the front (red plate) of the pump. Its
round metal surface MUST press firmly against the red plate or it will not function. If you can
slip a piece of paper between the switch and the red plate, it is not making sufficient contact.
Loosen the clamp and press the brackets further onto the pump so the contact is tight.
OPERATION The red push-button pops out if the pump runs dry. Push it in to reset the switch,
after water is restored.
A FLOAT SWITCH placed in the supply tank is an alternative to the Dry Run Switch. The
advantage is that it will reset itself when water rises, and will not allow the pump to lose prime.
The disadvantage is the need to run a power cable to the switch -- OK if distance is short.
Please call your dealer or the factory if you have questions.
WARNING Do NOT use a “LOSS OF PRIME” PRESSURE SWITCH for dry run protection.
This is a pressure switch with an automatic shut-off lever. It will NOT function with this type of
pump. Your pump will push sufficient air to maintain pressure, holding the switch on.
PLUMBING SYSTEM DESIGN
If you are not experienced in water supply design and installation, you may wish to seek
professional assistance. Many people are surprised to find how "complex" water system
design can be.
See diagrams on p. 20, for typical groundwater installations.
MINIMIZE SUCTION LIFT to just a few feet, if possible. The practical suction limit for any pump
is 20 vertical feet at sea level (subtract 1 ft. for every 1000 ft. of elevation). The more you
minimize suction lift, the more reliable and quiet your pump will be. Just be sure the motor will
not be submerged if the water level rises, or it will be ruined. Your pump may be placed
DOWNHILL from your water source, if feasible.
YOUR INTAKE PIPE may run any reasonable horizontal distance, although it is BEST TO
KEEP IT SHORT. (We know of installations where the pump is placed 200 feet from the water
source, using 1 1/2" pipe.) USE LARGE PIPE for the intake (1 to 1 1/2" for larger Slowpumps or
Booster Pump).
Slope the intake line from the water source UP toward the pump. AVOID HUMPS in the intake
line. They trap air pockets which can block the flow. AVOID LEAKS IN SUCTION LINE. They
are hard to locate and will cause constant problems.
= Page 3 =
4
INTAKE PIPE MUST BE SIZED GENEROUSLY to allow no more than a slight pressure drop at
peak flow rate, or pump will be noisey and will wear rapidly. USE PIPE REDUCER FITTINGS to
adapt your pump's inlet or outlet to larger pipe size where necessary. Excessive pipe sizing will
do no harm!
INTAKE MUST NOT BE RESTRICTED by undersized pipe, excessive suction lift, or a
CLOGGED FILTER. Excessive suction at the pump intake causes CAVITATION (formation and
implosion of vapor bubbles). This causes very loud buzzing noise and RAPID PUMP WEAR. A
slight buzzing noise is acceptable, if it cannot be avoided.
DO NOT USE THIN-WALL HOSE or soft tubing on the pump's intake. It may collapse under
suction and restrict the flow. Do not use polyethylene pipe (black flexible) for the suction either.
It is prone to slight leakage at the fittings.
INLINE FILTER should be mounted HORIZONTALLY and as low as possible. This prevents
any air trapped in it from blocking the water flow. Be sure to leave some space below it for a
pan, to catch water when replacing the filter cartridge.
FOOT VALVE is a check valve installed at the water intake. It is required in any case where the
pump is located higher than the low-water level in the source. We recommend a high quality
spring-loaded type to avoid loss of prime. A check valve allows water to flow one way and not
the other. Be sure to install it the right way! Our 30” Intake Filter or Fine Intake Strainer Foot
Valve accessory is recommended. These prevent debris from catching in the foot valve and
causing loss of prime.
REMOVE FOAM PLUGS BEFORE CONNECTING PIPES. New pumps are packed with foam
plugs to prevent contamination.
PRIMING YOUR PUMP: Priming a pump means filling its intake and suction line completely
with water. This must be done if the pump is mounted higher than the water source. A
removable plug or a valve must be installed at the highest point is in the suction plumbing.
Prime the pump and intake line by pouring water into the opening until it is completely full. Your
foot valve prevents loss of prime by not allowing water to flow back into the water source.
Your pump will create enough vacuum to SELF-PRIME to around 10 feet (less at high
elevations), but only when it is in new condition and wet inside. A priming plug is always
recommended if the pump is to be located higher than the water source. (EXCEPTION -- see
"Installation in Deep Well Casings"). You may use a good quality ball valve instead of a plug, if
frequent priming is expected.
A CHECK VALVE AT THE PUMP OUTLET is required if there is more than a 30 foot lift above
the pump, or in any pressurizing system. This allows the pump to start easier. It also prevents
back-flow when changing filter cartridges.
PIPE UNIONS: If you run rigid piping (copper or PVC) directly to the pump, unions are required.
Unions make pump replacement easy, without the need to cut and re-solder or re-glue the pipe.
"Copper Flex Connectors" commonly used for water heaters may be used instead. However:
Do NOT use them for the larger Slowpumps (2507, 2607) or Booster Pump. They are too
restrictive.
= Page 4 =
5
MOUNTING YOUR PUMP
Locate your pump in a cool place. Do not allow direct exposure to sunshine during operation, or
the motor may overheat. Allow free flow of air around the motor for cooling. SHELTER IT
FROM RAIN AND SUN, or it will be a mess in a few years.
The pump may be mounted horizontally or vertically. If vertically, FACE THE PUMP HEAD
DOWNWARD. RIGID MOUNTING IS NOT required in most installations. In a non-battery
system, starting is gradual and the pump does not jerk with the start. In a battery system, it will
jerk slightly, but simply mounting it to a small wooden board is sufficient to stabilize it. The
pump may be hung vertically on a rope. Observe the pump and see that it is not likely to
overstress or loosen pipes as it starts. DO NOT mount the pump directly to a wall or wood floor
in your home. It will increase the noise.
CHANGING PUMP HEAD POSITION: If you wish to face the pump's fittings sideways or
downward, you may rotate pump head to a different position by removing the four bolts that
secure the pump to the motor. If your pump looks like the picture on P.1, do this: Remove the
four hex-head bolts from the round plate, then rotate pump head to new position. REALIGN
THE PUMP AND MOTOR SHAFTS, or the coupler will bind and wear. This is simple. When
you remove the round plate, notice that the bolt holes are oversized for alignment adjustment.
Reposition as desired, but leave the bolts loose. BEFORE installing the pump, drop a teaspoon
of water into the inlet and run the pump (on 12 volts is OK for the 24v pumps). Slide the plate
around so it settles into the position where there is NO VIBRATION, then tighten the bolts firmly.
HANDLE YOUR PUMP CAREFULLY! Never hammer on it, clamp it in a vice or drop it. Pump-
motor alignment is critical. DO NOT DISTURB THE ALLEN-HEAD BOLTS holding the
mounting plate to the motor UNLESS you wish to rotate the pump head to a different position.
The shaft coupler between the motor and pump should turn easily using two fingers.
Sometimes after a period of dry storage, the pump will stick. If you can't turn the coupler, put a
bit of water in the pump intake and turn the coupler with pliers to "crack" it loose. Do this by
turning it BACKWARDS. If it sticks again, see “Troubleshooting”.
IF YOU ARE NOT EXPERIENCED WITH WATER SUPPLY
INSTALLATION, PLEASE CONSULT LOCAL SOURCES regarding:
(1) Freeze protection
(2) Choice and sizing of pipe
(3) Plumbing design in general.
INSTALLATION IN A DRILLED WELL CASING
INSIDE A 6-INCH WELL CASING, SPECIAL ELBOWS ADAPTERS are required. The elbows
fit 1/2" polyethylene (black flex) pipe. MEASURE CAREFULLY to determine the length of pipe
you need. SUBTRACT 1.5% TO ALLOW FOR PIPE AND ROPE STRETCH.
Assemble according to diagram. A priming plug is not needed. Before lowering the pump,
place the intake into a bucket of clean water and run the pump until water exits. Now it is
= Page 5 =
6
primed. A "pitless adapter" may be optimum for freeze protection. Check with your local well
supplier for details.
POLYETHYLENE PIPE comes in rolls, and is inexpensive and quite freeze-tolerant. Use with
plastic adapters and secure with ALL-STAINLESS hose clamps (obtain such clamps from a pipe
supplier rather than automotive supplier). If pipe does not stretch tightly over fittings, warm it
with a torch or hot water then tighten clamps firmly with a wrench. Use two clamps at each joint.
Keep extra clamps handy in case you strip one.
ELECTRICAL WIRING
WIRE SIZING: DON'T CHEAT YOURSELF with undersized wire! Your pump is wired with a
short length of #14 or #12 cable. This size is sufficient for short lengths only. Splice it to a
larger size of wire if your wire run is longer than 15 feet. Consult a low voltage wire size chart or
call your dealer or the factory for recommendations. Excessive voltage drop will slow the pump
down, but if it is unavoidable, don’t worry. It will NOT cause any harm to the motor.
BLACK WIRE = POSITIVE (+) WHITE WIRE = NEGATIVE (-) GREEN WIRE = GROUND
1400 & 2600-Series Slowpumps: Red = Positive Black = Negative
Reverse polarity will cause reverse rotation. This will not cause damage if done for a short time.
Reverse the wires if necessary so pump turns CLOCKWISE looking at the red face of the pump.
FUSE OR CIRCUIT BREAKER PROTECTION
FAILURE TO INSTALL A FUSE OR BREAKER equal to or less than
the motor's Max Amps rating WILL VOID YOUR WARRANTY.
If water flow becomes blocked, or if the pump jams or freezes and cannot turn freely, the motor
will draw excessive current. A fuse or circuit breaker will then break the circuit. Without such a
"safety valve", a minor fault can burn your motor and wiring.
Install a fuse or breaker with an AMP RATING close to the "MAX AMPS" rating of your motor,
OR LESS (but not more higher). If a Linear Current Booster is being used (for array-direct
Slowpumps) install the fuse between the booster and the pump. Use the rating recommended
for the booster or for the pump, WHICHEVER IS LESS. This fuse will protect the booster as
well as the motor and wiring from overload.
FUSES: Use a “time-delay” type. The 3" paper cartridge type is good, and may be installed into
a raintight disconnect switch available at any electric supplier. An automotive in-line fuse holder
is fine for 12 or 24V systems. Automotive blade fuses (type ATC) are prefered over glass fuses.
They have sufficient time-delay. (Time-delay glass fuses are available from ELECTRONIC
suppliers only, not automotive.) Use good quality fuse holders, protected from weather. Keep
spare fuses handy. Never substitute a larger fuse!
CIRCUIT BREAKERS: Most AC breakers cannot be used for low voltage DC circuits. We
recommend only the SQUARE-D® QO or QB-series which been rated safe up to 48 volts DC. A
10 amp size is available, but not in most stores. It may be ordered from your PV dealer or from
an electric supplier.
= Page 6 =
7
Install the fuse or breaker at the power source, to protect the wiring as well as the motor. If the
circuit is protected by a breaker, then any additional fuse may be installed at the motor.
THERMAL OVERLOAD
If your pump resembles the illustration on P.1, a THERMAL SWITCH is mounted on the rear of
the motor (inside the white cap) to shut off the motor if it approaches an overheat condition. If
this happens, it will turn back on after a cooling period of about 20 minutes. If overheating
occurs during normal operation of the pump, it may be because it is working beyond it’s
capacity. See Troubleshooting.
The Flowlight Booster Pump, Standard Model may overheat if it is running for more than 20
minutes at a pressure exceeding 50 PSI. It will cool and reset automatically.
GROUNDING and LIGHTNING PROTECTION:
A long wire run may act like an antenna, receiving induced surges of high voltage when lightning
is present. Proper grounding will greatly reduce risk of lightning damage to your power system.
A proper ground system consists of a minimum of one 8 ft. copper-plated ground rod driven into
the ground, preferably in a moist spot close to the PV array. Or, if you have a steel well casing,
drill and tap a bolt hold to make good contact to it.
In a dry, lightning-prone location, use more than one ground rod at least 10 ft. apart. Bury bare
copper wire between them. Use min. #8 ground wire (larger for distances exceeding 20 ft.). In
a rocky location, where ground rods can't be driven, bury (as much as feasible) 150 feet (total)
of bare copper wire, radiating out in two or more directions from the PV array. Try to contact
moist earth as much as possible. Use only the copper or bronze electrical connectors designed
for grounding application, and BE SURE ALL CONNECTIONS ARE TIGHT.
Connect your ground system to the METALLIC FRAME of your PV array via min. #8 copper
wire. Also ground metallic support structures and electrical enclosures. For non-battery pumps,
we have observed the least lightning damage where only the mechanical structure is grounded -
- NOT an electrical conductor. This may vary from electrical codes. Call the manufacturer of
your controller, if you have questions.
WATER LEVEL & FLOW CONTROL
FLOAT SWITCHES/WATER LEVEL SENSORS: These are devices that sense high or low
water level and switch your pump on and off. Ask your dealer or factory about these. Most
switches rated for 15 AMPS at 230 VAC are fine for your DC pump.
FLOAT CONTROL IN WATER SOURCE may be used if dropping water level is causing dry run
or excessive suction (noise due to cavitation).
FLOAT CONTROL IN STORAGE TANK may be used to turn pump off when tank fills. This
eliminates tank overflow and reduces pump wear and filter changing.
REMOTE FLOAT CONTROL when tank is a LONG DISTANCE from pump may be done in
three ways:
(1) Small wire buried from tank/float switch to pump actuates a relay at the pump.
(2) Very small wire from sensor in tank actuates "Water Level Sensor" option in your pump
controller (LCB). This is for non-battery systems only.
= Page 7 =
8
(3) Float valve in tank restricts flow. Pressure builds up and actuates pressure switch at
pump. Small captive-air pressure tank is necessary at pump to prevent "switch chatter".
Contact your dealer or the factory for further advice.
FLOW RESTRICTION MUST NOT BE USED as a method to reduce your pump's flow rate. It
may result in excessive pressure build-up and current draw.
Flowlight ®Booster Pump Installation
For Pressurizing Systems
A PRESSURE TANK IS REQUIRED with a Booster Pump system. PRESSURE TANKS are
available from local water supply dealers. Use the largest tank that you are willing to buy. 40
gallon size is typical -- it allows you about 12 gallons of water between pump cycles. Those 12
gallons may be drawn at a higher flow rate than the pump produces. A large pressure tank will
minimize on/off cycling of the pump. In a typical household of more than four people, a tank of
at least 60 gallons is recommended. The bigger the better! More than one tank may be
connected. They need not be the same size.
A PRE-CHARGED "CAPTIVE AIR" TANK is recommended. Cheaper "galvanized tanks"
require periodic recharging, store less water between cycles, and don't last as long. PROPER
PRE-CHARGE IS ESSENTIAL. Follow the instructions that come with your pressure tank –
With presure discharged from the tank, adjust pre-charge to 2-3 PSI below cut-in pressure. This
will assure that you get the best performance from your system.
Installation from cistern or
storage tank where pump is
higher than the water source
= Page 8 =
9
NOTE: It is preferable to place the pump LOWER than the water level in the tank. This
illustrates an alternative, not an ideal. Note the upward rise of the suction pipe, the high position
of the priming plug, and the horizontal position of the filter. These measures help prevent air
entrapment that restricts flow and causes pump noise.
Follow your pressure switch instructions for wiring. Use the flexible hose that comes with your
Booster Pump (cut it into two sections). Our Easy Installation Kit contains the tee fitting at the
tank, a DC-rated pressure switch, and all of the small parts shown between the pump and the
house plumbing. See PRESSURE SWITCH DIAGRAM on PAGE 20
Typical Flowlight Booster Pump installation
Illustration by Home Power Magazine
PRESSURE SWITCH ADJUSTMENT: Switch settings determine the pressure range of your
system. To conserve energy, set the pressure as LOW as feasible. This will also prevent the
motor from overheating if you run it for long periods -- sprinkling, for example. Low pressure
(even 15-20 PSI) may deliver excellent water flow IF your plumbing and hoses are sized larger
than minimum. If not yet plumbed, use at least one size larger pipe than conventional, and
avoid restrictive connections such as 3/8" tubing often used to feed sinks.
Adjustment: Start with the standard setting (usually 30/50 PSI). Reduce the pressure according
to your requirements, if you wish. It is wise to measure the current used by your pump (with an
amp meter in series with the line, your system metering). Current draw will rise in direct
proportion to outlet pressure. Pressure should NOT be set beyond 50 PSI MAXIMUM (65 PSI
with 2910 Model) or loss of efficiency and motor over-heating will result. IMPORTANT: After
any change to your cut-in pressure, you need to readjust the pressure tank pre-charge.
= Page 9 =
10
If you are raising water vertically AND pressurizing, note the relationship: 2.31 ft. = 1 PSI.
Example: A pump that lifts 23 vertical feet and pressurizes to 30 PSI must pump a total of 40
PSI. Total lift = vertical distance from water surface to pressure tank.
WARNING: INSTALL THE PRESSURE RELIEF VALVE INCLUDED WITH YOUR PUMP!
Flowlight Booster Pumps are supplied with a 75 PSI Pressure Relief Valve as a safety feature.
If your pressure switch fails, EXCESSIVE PRESSURE may cause your tank or piping to burst
and flood your home. (A properly sized fuse or circuit breaker should shut pump off before relief
valve opens BUT many breakers are not accurate, and the proper fuse may not always be
present.)
INSTALL THE PRESSURE RELIEF VALVE near your pressure tank (at the "Accessory Tee"
shown in diagram). Run a pipe or hose from its outlet to a drain or drain pipe or to the outdoors
where water can drain away safely.
A GATE VALVE and DRAIN VALVE are recommended (see diagram) for convenience during
system shut-down. The drain valve is simply a garden hose outlet which allows easy draining of
the system. It also allows water delivery by hose while water is shut off to the house during
installation or repairs to plumbing.
EASY INSTALLATION KIT IS AVAILABLE!
If you have not yet purchased the small parts you need to install your Booster Pump, you can
save time and confusion by purchasing our convenient Easy Installation Kit. Pipe components
are brass to resist corrosion. The kit includes pressure switch, pressure gauge, tank tee, shutoff
(ball) valve and hose bib (drain valve) plus the necessary pipe nipples. Order Dankoff Solar Item
#20200
VENTILATION SLOTS are located on bottom of motor for cooling (Standard Model Booster
Pump only). If you are concerned with insects building nests inside your motor, glue some
screen over the slots. Silicone sealant works best for this.
FLOWLIGHT BOOSTER PUMP requires a BATTERY SYSTEM, NOT A PV ARRAY-DIRECT
installation. PV ARRAY voltage may exceed 15V and overspeed the pump.
= Page 10 =
11
SOLAR SLOWPUMP — POWER CONTROL for
ARRAY-DIRECT (NON-BATTERY) OPERATION
When working against a constant head (vertical lift) Solar Slowpump requires nearly constant
current, regardless of the voltage/speed. When low light conditions are present, the PV array
cannot supply full current. The voltage will drop to nearly zero, and the pump will “stall” (like a
truck trying to start in 4th gear). The remedy is either to add a PUMP CONTROLLER, also
called LINEAR CURRENT BOOSTER (LCB) to your system. This device will match the power
source to the load by transforming the voltage down while increasing the current delivered to the
motor (like an automatic transmission). If you are not using a controller in your non-battery
system, contact your dealer. It will greatly improve low-light performance.
Remote Tank Float Switch: See your controller instructions. Float switch
must MAKE contact on rise, to turn the pump OFF. This is opposite of
normal action, so your float switch may be labeled “pump down to empty”.
System Wiring for Typical Slowpump Installation
-- Non-battery System --
Earth
Ground
Controller
(LCB)
-
- +
+
Installing a Solar Tracker? Use stranded
wire for flexibility. Secure the wires to
tracker with plenty of tape. Make a long
slack loop to allow free motion of tracker.
“Series” Wiring is shown, for nominal 24V
system: Voltage from panels will read 40V
when disconnected (open circuit), and
about 30V while pumping.
For 12 Volts, use a single panel, or wire
panels in parallel (+ to +, - to -).
•
••
• ••
on
off
for backup power or testing using a battery,
hook jumper wires here , not to controller input.
Pump
The proper fuse must be
inserted inside the LCB to
protect the pump from
overload.
PV
Array
= Page 11 =
12
WATER USAGE
WATER CONSERVATION = ENERGY CONSERVATION
+ LESS FILTER MAINTENANCE
TOILETS: A 1.6-gallon flush toilet may reduce total domestic water consumption by 50%
compared with typical 4-5 gallon toilets. They are now standard in U.S.A.
IRRIGATION SYSTEMS: Many drip, trickle or flood irrigation systems will function on LOW
PRESSURE. It is wasteful of energy to supply pressurized water where it is not required. You
may wish to arrange separate gravity flow from your water source or storage tank, if possible.
Or, if a small amount of lift/pressure is required, consider a low-pressure DC pump such as a
marine bilge or circulator pump.
LOW FLOW SHOWER HEADS are recommended IF you are running 30-50 PSI pressure
range. At lower pressures, they may not provide adequate flow.
FREEZE PROTECTION
If freezing of your outlet pipe is to be expected, you may avoid the frequent necessity of
replacing fuses or resetting your breaker by installing an ADJUSTABLE PRESSURE RELIEF
VALVE at the pump outlet. This will allow water to flow back into the well when outlet pipe is
blocked. Order the valve from your dealer or any electric or plumbing supplier (Grainger's part
num
Dankoff Solar Booster Pumps Installation Manual
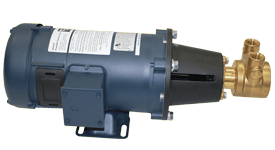